Automated guided vehicles provide relief in beverage warehouses
AGVs address labor concerns, safety, quality control and more

Image courtesy of Dematic
The chorus for Dolly Parton’s hit song “9 to 5” harmonizes, “Working nine to five, what a way to make a livin’/Barely getting’ by, it’s all taking’ and no givin’,” reflecting a challenge of a workplace summed up by standardized work hours. Yet, when it comes to automated solutions, operations are seeing the potential go beyond standardized work hours.
These solutions also are appealing to beverage warehouses as today’s labor market continues to be a pain point for operations.
“The labor shortage remains a significant challenge for warehousing operations ― 52% of operations say that a talent shortage is one of their biggest challenges, and the total labor force participation is only 62.5%, according to the 2024 MHI Industry Report,” says Kevin McWilliams, director of major accounts at Yale Life Truck Technologies, Greenville, N.C. “Plus, warehouse labor turnover has hovered around 40% for the last several years. Because the labor market for warehouse workers is so competitive, it’s difficult for operations to hire to optimal staffing levels and hold onto those workers. That in turn makes it very difficult for operations to manage costs and keep pace with demanding expectations for delivery.”
McWilliams adds that as the labor pool has become more transient, safety issues have become an even greater concern.
“According to the Bureau of Labor Statistics, warehouses experience injury and illness rates that are higher than private industry overall and, in some sectors, more than twice the rate of private industry,” he explains. “In response to these rates, the Occupational Safety and Health Administration (OSHA) has announced a three-year national emphasis program to reduce and prevent workplace hazards in warehouses and distribution centers.”
With operations feeling the strain because of labor shortages, fulfillment of orders also are being challenged. As a result, customers are feeling frustrated when deliveries arrive behind schedule.
“The pressure to meet tight deadlines is causing an increase in errors during picking and packing, which requires reworks and damages customer trust,” says Doug Houghton, 4.0 facility development manager at JBT Corp. – Automated Systems, Chalfont, Penn. “With an understaffed workforce, warehouses struggle to keep up with the demand, leading to burnout among existing employees and further exacerbating the labor shortage problem.
“These labor shortages increase the competition for the available labor,” he continues. “This competition drives up labor costs and increases employee turnover. Labor generally makes up 60-65% of the total cost of warehouse fulfillment (not including shipping). While hourly labor rates have increased 10% to 15% in the past several years.”
Houghton adds that as the labor pool ages, warehouse operations are finding a smaller pool from which to source with younger generations.
“There is a reduced desire in the younger workers to work second and third shifts and the fierce competition for workers is forcing companies to hire less experienced staff,” he says. “This can result in a rise in product loss and damage, safety hazards, misdirected shipments, and unfilled orders. Additionally, customer returns may also increase.”
These challenges have been present since before the pandemic, but after the pandemic, the issue proliferated.
“Both the availability and cost of labor were challenges before the pandemic,” says Lorne Weeter, vice president of sales and mobile automation of Americas at Dematic Corp., Atlanta. “Since the pandemic, labor has become an even larger challenge. In addition, labor availability is not the only issue; the skill level of labor available to work in warehouses is becoming a challenge as well. For functions such as operating manual or automated forklifts, workers must be trained to ensure safe and efficient operations. Without skilled drivers, inventory, quality, and safety issues can occur.”
Turning to automation
Given all the complexities with today’s labor force, solutions like automated guided vehicles (AGVs) are providing warehouses the relief they have been looking for.
“Operations are turning to automated lift trucks to relieve their dependency on the transient labor pool as they strive to meet escalating demand for high throughput and fast delivery,” Yale’s McWilliams says. “Automated lift trucks are especially useful in common repetitive tasks and long runs, allowing workers to be redirected to more meaningful, value-added tasks that can keep employees more satisfied and help curb turnover.”
JBT’s Houghton explains that AGVs can take over repetitive tasks, like transporting full pallets.
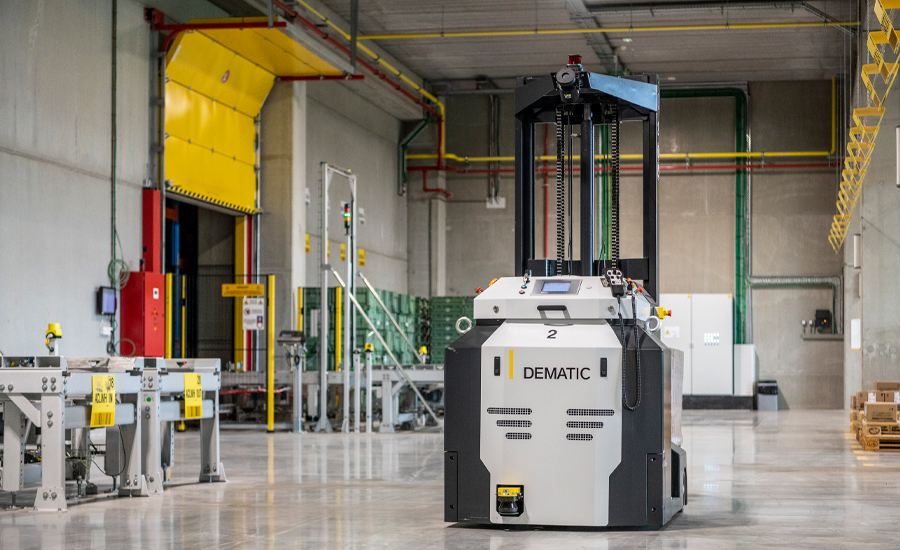
“This frees up human workers to focus on higher-value activities that require problem-solving skills and dexterity, such as complex order picking and quality control inspections,” he says. “Unlike human workers, AGVs can operate 24/7 without breaks, significantly increasing the overall throughput of the warehouse.
“They also follow precisely programmed routes, minimizing the risk of human error in material handling and ensuring greater accuracy in order fulfillment,” Houghton continues. “In addition, automation represents a stable, predictable cost structure that will not rise and fall as the competition for labor changes.”
Dematic’s Weeter echoes these sentiments regarding the plethora of benefits.
“AGVs can operate three shifts a day, 24 hours a day,” he says. “With opportunity battery charging or automated battery exchange (ABEX), AGVs need limited breaks. Thus, a fleet of AGVs can operate with minimal manual intervention. This allows the warehouse to continuously operate and easily adapt to changes in orders.”
Additionally, Weeter notes that AGVs can address skilled labor challenges in the areas of inventory, quality issues and safety concerns.
“With AGVs, the WMS (warehouse management system) or WCS (warehouse control system) directs the AGVs to store or pick the pallet in the correct location,” he explains. “This ensures inventory accuracy and eliminates the wasted labor needed to resolve issues.”
In terms of quality, Weeter points to the sensors that can help avoid potential damage that comes with lift trucks.
“Manual forklift operators can damage both the SKUs on the pallet and the surrounding infrastructure (e.g., racks, columns, other equipment),” he says. “Many operations see a 10-15% reduction in quality costs by implementing AGVs. AGVs use sensors to identify collision points and then either move around the obstruction or stop before a collision, and notify an operator to resolve the issue.”
But more important than protecting product is protecting the people in the warehouse, and AGVs also can be a vital asset in this area.
“In North America, AGVs follow the ANSI/ITSDF B56.5-2019 safety standard,” Weeter says. “Using dynamic safety zones, AGVs can detect both pedestrians and fixed objects to prevent collisions.”
In addition to all these aspects, Yale’s McWilliams notes that AGVs productivity attributes allow operations to also reduce costs.
“Such reliable efficiency gains might seem like they would come at a steep price, but the truth is that autonomous lift trucks can help reduce operating costs with a lower total cost of ownership and a clear return on investment,” he says. “Plus, the solutions can allow some warehouses to decrease spending on labor and maintenance ― a major opportunity for operations facing financial pressures.”
Informed decisions
Given all these factors, it’s understandable why operation managers would look to invest in AGV technology. Like any major investment, expert highlight the importance of considering a host of factors.
“Warehouse decision-makers must carefully consider several factors before investing in or upgrading their AGV systems,” JBT’s Houghton explains. “One crucial aspect is the warehouse layout. Warehouses optimized for manual operations often cannot be directly automated without some level of modification. AGVs function most effectively in well-organized and clearly defined warehouse spaces. In some cases, remodeling the warehouse layout might be necessary to optimize the utilization of AGVs.
“The initial investment in AGVs needs to be carefully evaluated against the potential long-term benefits, such as labor cost savings, reduction in product damage and significant improvements in efficiency,” he continues. “Scalability is another important consideration. Choosing an AGV system that can be easily expanded as the warehouse grows and its needs evolve is crucial for future-proofing the investment. Finally, warehouse decision-makers should factor in the maintenance costs associated with AGVs to ensure the long-term sustainability of this technological integration.”
Yale’s McWilliams echoes similar sentiments, adding that IT is another important consideration.
“While interfacing robotics software with the facility’s warehouse management system (WMS) is not required, that process can enable more seamless operation and tightly managed workflows,” he explains. “Enlisting IT early in the process helps determine requirements or reveal potential capacity issues. Automated lift trucks can handle basic point-to-point transportation tasks without requiring such a software integration, enabling operations to get robotics up and running quickly and more simply. Compared to traditional AGVs, automated lift trucks offer lower costs to handle routine maintenance and resolve unexpected issues, since they are standard lift trucks with automation added.”
McWilliams adds that this can allow operations to turn to local dealer personnel to provide service, without downtime and expenses that often come with specialized technicians.
“These dealers are also able to provide parts and training support when needed, giving warehouses a single-source provider for most aftermarket functions,” he says.
Dematic’s Weeter further points to the importance of prepping for the addition of AGVs into a warehouse.
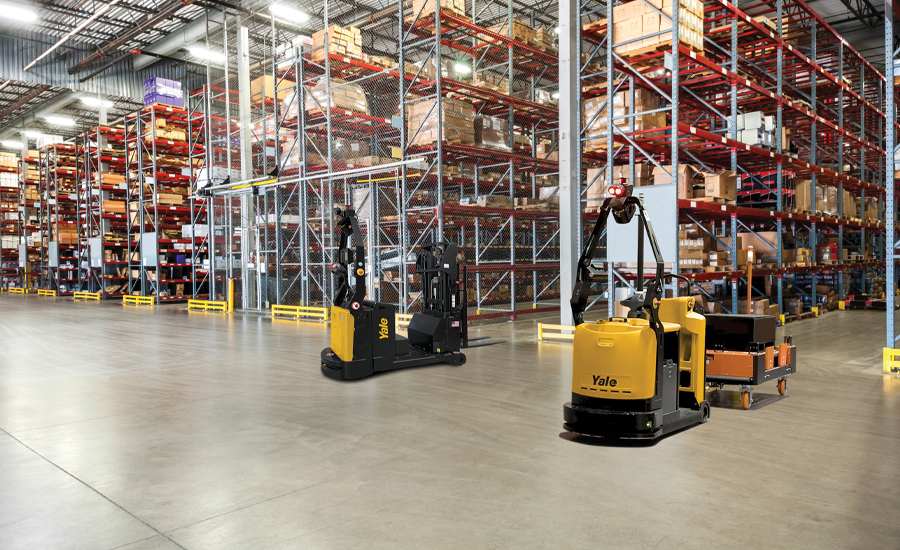
“Operational readiness must be considered during the installation, commissioning, and acceptance of an AGV system,” he says. “Additionally, as with almost all automation, start-up should be ramped up over several months. Optimization efforts after ramp-up should also be scheduled to further improve operations.”
As more warehouses embrace automation in its variety of forms, experts anticipate AGVs will play a bigger role in the years to come.
“With the advent of AI and self-driving vehicle technology (sensors and software), AGVs will become even more automated, with the ability to detect and resolve path anomalies or pallet issues (e.g., pallet quality, hanging stretch wrap, broken boards, skewed pallets),” Weeter says. “Specifically for the beverage industry, AGVs will be able to transport and store over 4,000 pounds at heights over 32 feet with minimal aisle width. This will increase storage density in smaller warehouses closer to customers.
“AGVs are also now able to perform both trailer unloading and loading for the beverage industry,” he continues. “Trailer unloading must occur quickly to turn the dock doors, while trailer loading requires vehicle traffic management and close coordination with the WMS/WCS to create the proper trailer loading sequence. For example, reverse-truck-loading or pin-wheeling. Both trailer loading and unloading can handle stacked pallets to increase operational efficiency.”
JBT’s Houghton also remains optimistic about the future of AGVs, noting their growth throughout beverage warehouses.
“The heavy, predictable dimensions, and date sensitivity of a typical beverage pallet makes it ideal for automation,” he says. “As the labor shortage continues to tighten, AGVs are becoming a standard feature in most beverage warehouses. Many major beverage customers are in large scale deployments of AGVs across their whole distribution network. Beverage companies that are just starting their automation journey are already 10 years behind the leaders.
“We can expect to see even more intelligent and adaptable AGVs with advanced capabilities like machine learning and self-diagnostics,” Houghton continues. “These advancements will further enhance the efficiency and automation of warehouse operations and propel AGVs into new applications such as fully automated trailer loading and unloading. The future might also see AGVs working collaboratively with robots to automate an even wider range of tasks within beverage warehouses, creating a highly integrated and streamlined system for optimal efficiency.”
Yale’s McWilliams adds that the advancements taking place within AGVs suggest much more is in store for those looking to make the investment that will help not just operations but the people working alongside the technology.
“Automated lift trucks are still a developing technology, and as such, these solutions are becoming simpler, more cost-effective and more reliable with newer generations,” he says. “It is also worth noting that automation does not automatically mean robotics like automated lift trucks. Operator assistance technologies can include automation technologies that help improve safety in the warehouse while keeping a human operator in control of the lift truck, helping to reinforce best practices and improve operator confidence and performance.”
Looking for a reprint of this article?
From high-res PDFs to custom plaques, order your copy today!