Predicting the unpredictable
Differences between predictive, preventative fleet maintenance remain vast

In last month’s issue of Beverage Industry, we talked a great deal about preventive maintenance and the pitfalls to avoid when developing proper protocols for such. Now, it’s time to tackle a separate concept that too often gets confused with preventive maintenance, but is an entirely different approach all together: predictive maintenance.
There are a number of key elements that distinguish preventive from predictive maintenance.
For starters, preventive maintenance is typically based on a pre-ordained timetable based on factors like average miles driven by a particular vehicle, as well as overall hours spent on the road. It’s largely schedule-driven and time-based, involving regular maintenance at prescribed intervals, whether or not an operational issue is imminent.

By contrast, predictive maintenance is data-driven and condition-based, relying on real-time monitoring and more advanced technologies like Internet-of-Things (IoT) sensors, machine learning and data analytics to predict failures and perform maintenance only when necessary.
“[Predictive maintenance] can generate long-term cost-savings and optimize resource use, but requires a much larger investment,” says Andrew Bartholomew, product marketing analyst at Fleetio, Birmingham, AL.
On the other hand, preventive maintenance, Bartholomew says, is easier and cheaper to implement.
“Preventive maintenance … is easier to adopt and can be a good stepping stone to predictive maintenance,” he notes. “Preventive maintenance reduces the risk of downtime and extends asset life through routine servicing.”
Despite the greater investment cost of predictive maintenance, implementing it can generate significant savings and downtime reduction. In fact, the U.S. Department of Energy estimates that functional predictive maintenance can help fleets realize a reduction in maintenance costs of up to 25 to 30%. Additionally, fleets can achieve a 35 to 45% reduction in downtime.
“Predictive maintenance for trucks is particularly valuable for components that are operationally critical and can be predicted in a cost-effective manner,” Bartholomew adds. “Examples include the engine, brakes, tires and battery. In the engine and powertrain, sensors can monitor oil quality, vibration patterns and component wear to prevent failures.”
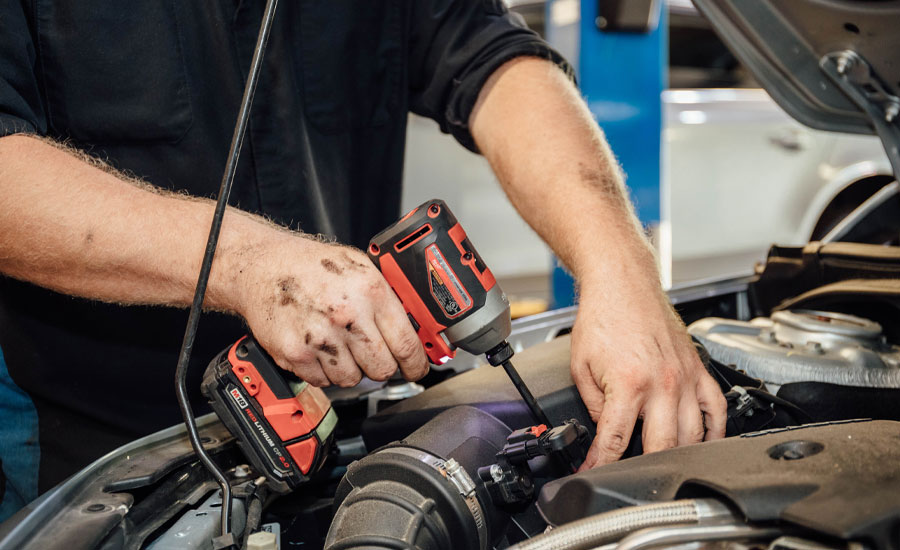
Brake systems, he explains, benefit from sensors that track brake pad wear and brake fluid quality, ensuring that they’re replaced in a timely manner. Meanwhile, tire pressure, temperature and tread-depth sensors help predict tire failures and optimize replacement schedules.
“Monitoring battery health and performance can prevent costly electrical failures in the battery, alternator and starter motor,” Bartholomew continues.
Predictive technologies continue to evolve and improve, and likely have already done so significantly in the brief timespan between the writing of this article and its subsequent publication.
Predictive maintenance is not necessarily a replacement for preventative maintenance, as the two can complement each other.
“By continuously monitoring the key components through IoT sensors, predictive maintenance allows for maintenance tasks to be performed just before a failure is likely to occur,” Bartholomew points out. “When paired with preventive maintenance, which schedules routine checks and services at regular intervals, fleet managers can create a robust maintenance strategy.
This combination ensures that while regular preventive tasks keep the fleet in good condition, predictive maintenances addresses specific issues as they arise, further minimizing unexpected breakdowns and optimizing maintenance efforts. This dual approach enhances the reliability and efficiency of the fleet, translating into substantial cost savings and improved operational uptime.”
Looking for a reprint of this article?
From high-res PDFs to custom plaques, order your copy today!