Operations
Warehouse operations turning to robotics to tackle labor challenges
Artificial intelligence, cobots deliver varying solutions

Image courtesy of Swisslog
In sports, optimum speed gives athletes an advantage. For example, a faster athlete might be able to get to a ball more quickly than a competitor or outrun an opponent. As such, athletes in most sports highly value speed. In beverage operations, where optimum speed also brings advantage, experts note that artificial intelligence (AI) is making the future of warehouses more dynamic.
With eCommerce and consumer preferences radically transforming the market, fulfillment speed, agility and accuracy are becoming imperative, notes Mark Koffarnus, major accounts manager at Greenville, N.C.-based Yale Materials Handling Corp.
As order-volumes rise and expectations evolve, “it’s crucial for beverage operations to enhance productivity to meet these demands while also managing and utilizing scarce labor resources effectively,” he says. “With 40% of businesses saying operator turnover is their greatest challenge, it’s easy to understand why interest in and adoption of robotics has accelerated in recent years.”
As labor issues begin to normalize in other industries, “the fulfillment industry is predicted to face continued labor shortages,” notes Bedford, Mass.-based Berkshire Grey in its “2022 State of Retail & eCommerce Fulfillment Report.”

Image courtesy of FANUC America Corp.
These shortages “will only compound in the coming years as a result of an aging workforce, pandemic-related illness and reskilling, low birth rates, and generational shifts in employment preferences,” it states.
Conducted in partnership with Hanover Research, the Berkshire study surveyed Chief Supply Chain Officers at retail and eCommerce businesses, as well as additional topics including automation, costs, pain points, and predicted areas of industry growth.
The following are some of the key findings from that study:
- Robotics are a solution to the growing gap in younger job applicants: Nearly three-quarters (71%) of executives believe robotics automation is necessary to counter reduced applications from younger generations and mitigate the long-term labor shortage.
- Robotics improves talent retention: Over half (51%) of executives believe implementing automation will increase employee satisfaction, and 43% believe it will lead to a decrease in employee turnover.
Robotics key role within DTC channel
With direct-to-consumer (DTC) on the rise, experts note that this channel looks completely different from direct-to-store.
Alongside eCommerce driving a retail landscape evolution, is the move into DTC sales by manufacturers, notes Grant Beringer, vice president of integrated systems at Swisslog, Newport News, Va.
“SKU growth and smaller store formats are limiting shelf space and forcing less inventory to be carried per SKU while keeping or increasing the overall SKU count,” he explains. “Grocers and retailers will be challenged to accept cases of slower moving products at the store level and will instead have to push for single item replenishment of those products. Simultaneously, manufacturers recognize the opportunity in eCommerce and will need to support their entry into [business-to-consumer] (B2C) from their centralized warehouses by adding item-level handling capabilities within these facilities.
“The result is the transformation of many warehouses as they integrate new processes and technologies to enable efficient item picking,” Beringer continues. “Goods-to-person technologies, such as cube-based automated storage and retrieval systems and mobile autonomous robots are finding homes in warehouses that had previously only supported bulk handling of products.”
Where manufacturers are scrambling to automate on the traditional line, “they are keeping the DTC channel top of mind,” says Wes Garrett, senior account manager of authorized systems integrators at FANUC America Corp., Rochester Hills, Mich.
“As the DTC channel grows, robotics will be a key piece of the automation utilized,” he adds.
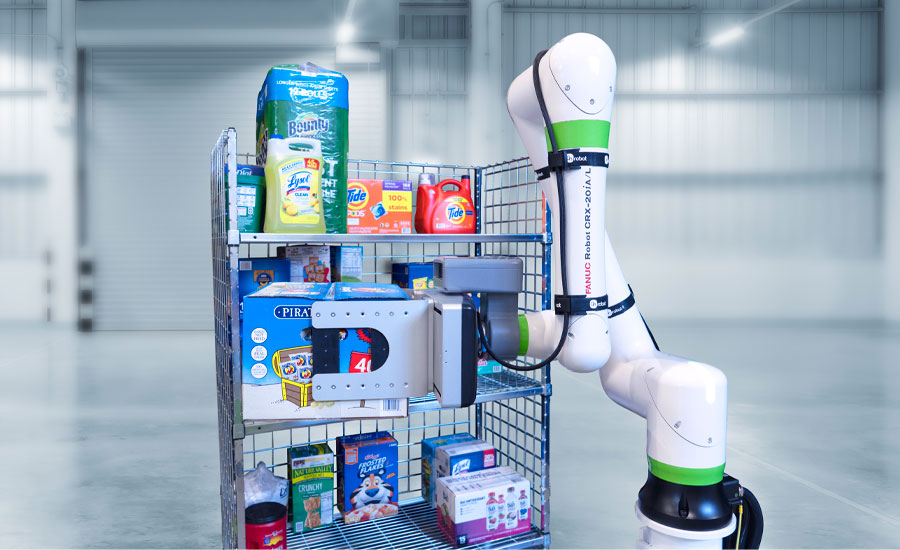
Image courtesy of FANUC America Corp.
New technology brings further advantage
With more advanced gripping and vision systems, experts note that newer generation robotic picking solutions offer high operational reliability.
Stephen Dryer, senior global product manager at Mt. Washington, Ky.-based MHS, highlights how AI can provide visual perception to identify and classify individual items without explicit programming.
“AI can be used to tackle problems of path planning, dexterity and grasping by learning based on previous pick attempts or by supervised learning,” Dryer says. “This combination enables robotics to handle highly variable work, such as singulating various parcels for downstream automation or picking items for individual eCommerce orders.
“These advancements have enabled automated alternatives to manual processes, helping to alleviate operations from labor shortages and rising costs,” he continues. “These advancements are especially well-suited for warehouse and distribution center environments due to the variability of work pieces, such as bagged items, corrugate cases or other types of packages ― the robot handles thanks to vision technology that provides output on par with almost anything a person can see.”
Yale’s Koffarnus notes that with vision technologies finding their way to robotic lift trucks, these technologies can help to detect obstacles, such as a stray box in the truck’s path of travel. Such technologies can “even validate whether an unexpected pallet is in the storage position where it is supposed to place one,” Koffarnus says.
“Thanks to navigation technology and site-specific programming, robotic lift trucks can adapt to surroundings and real-time conditions starting on day one strictly following safety protocols,” he adds. “This can help reduce the risk of accidents and collisions, without the extensive onboarding and training required by new operators.
“Robotic lift trucks are also now capable of addressing not just horizontal storage tasks, but also vertical ones, and some robotic trucks for vertical workflows can also serve double-deep pallet storage locations,” he continues. “This allows for improved productivity in high-density warehouses, which is especially helpful as warehouse space has become more expensive and even harder to find in recent years.”
Cobot systems offer safe, efficient human interactions
Like other forms of automation, experts note that cobot systems can help operations reduce labor dependency and increase productivity.
“It all comes down to what you’re looking for in a system and the needs of your operation,” MHS’ Dryer says. “Whether it’s cobots or something else, the focus of any automation project should be on solving the challenge using the right tools.
“One way to look at this is the degree of human interaction — cobot systems are designed to have interaction with humans,” he continues. “While cobots can be the right fit for certain applications, the decision to use either a cobot or an industrial robot working without a human counterpart must consider a number of factors such as performance, cost and system footprint.”
As cobot systems include the ability for operators to work alongside it, FANUC’s Garret notes that additional safety hardware works to ensure the system is safe.
“This hardware could be area scanners, force sensors within the arm, light curtains, etc.,” he says. “The safety hardware allows the cobot to operate outside of a fence in a collaborative application if space is tight.
“They can also allow for more flexibility, meaning that since they are lightweight and typically run on 110 [volt] power, they are very practical to move from line to line,” he continues.
Technology, ease-of-use continue to advance
As automated solutions can lower operational costs, increase speed and efficiency, experts highlight the various advantages for beverage operations.
“Robotic mixed case palletizing is designed to grow as the business grows and can be implemented starting with semi-automated modules, which are later transformed into fully automated modules,” Swisslog’s Beringer notes. “Beverage-makers could efficiently process and handle up to 1,000 units per hour, per robot.
“Robotic case picking, such as Swisslog’s ACPaQ solution, further enhances warehouse operations and allows mixed SKU palletizing of large volumes and SKU varieties,” he continues. These types of robotic systems can be connected to larger ASRS systems such as shuttle systems and can handle almost all types of cartons, shrink wrapped or foiled packages and pallet types for fully automated order picking.”
Because robotic solutions can automate a number of applications within the warehouse, MHS’ Dryer notes that mundane, repetitive tasks easily can be automated.
“This allows them to assign labor to more valuable roles, helping reduce turnover while boosting productivity in those more repetitive processes,” Dryer says. “Adopting robotics can also help to reduce the number of workplace injuries, as manually lifting items and twisting in awkward ways can lead to repetitive stress injuries. Each one of those injuries can come with thousands of dollars in medical and legal costs, OSHA fines and lost productivity.
“Automating those processes allows for productivity to remain high and costs to be controlled,” he continues.
Whereas introducing robotics into beverage operations might be a daunting challenge, experts note that an operation team plan and investment in resources and maintenance practices can help overcome challenges.
“Systems can be designed and started up using manual picking operations with the view to add on robotics as your business and capability grows; robotic modules can be converted from manual to automated as your volumes increase,” Swisslog’s Beringer says. “Most importantly, a trusted automation partner is key when implementing automation.
“As the technology and ease-of-use continues to advance, many companies are seeing robotics as a viable business option,” he continues. “In fact, the technology is even becoming a powerful tool in attracting and retaining the skilled labor many companies need.”
With integrators to help clients navigate that adoption process, “the right partner should make that journey much easier for the end-user,” MHS’ Dryer adds.
“Operations are going to have questions about how to incorporate robotics into their workflows, then trials to work through during test or pilot phases, and eventually adjustments or enhancements that they might want to make as their business changes over time,” Dryer notes. “In fact, many robotic solutions, including AMRs, are easily scalable, meaning operations can add vehicles, change paths and shift workstations without shutting down the whole facility.
“An integrator can really be a consultative resource not only when operations are first implementing and learning how to run their robotics, but also to help them optimize the solution to meet changing needs and maximize the ROI of the system through its entire lifecycle,” he concludes.
Looking for a reprint of this article?
From high-res PDFs to custom plaques, order your copy today!