Warehouse
WMS, WCS help warehouses “take it to the limit”
Warehouse execution systems expected to grow 12% through 2027
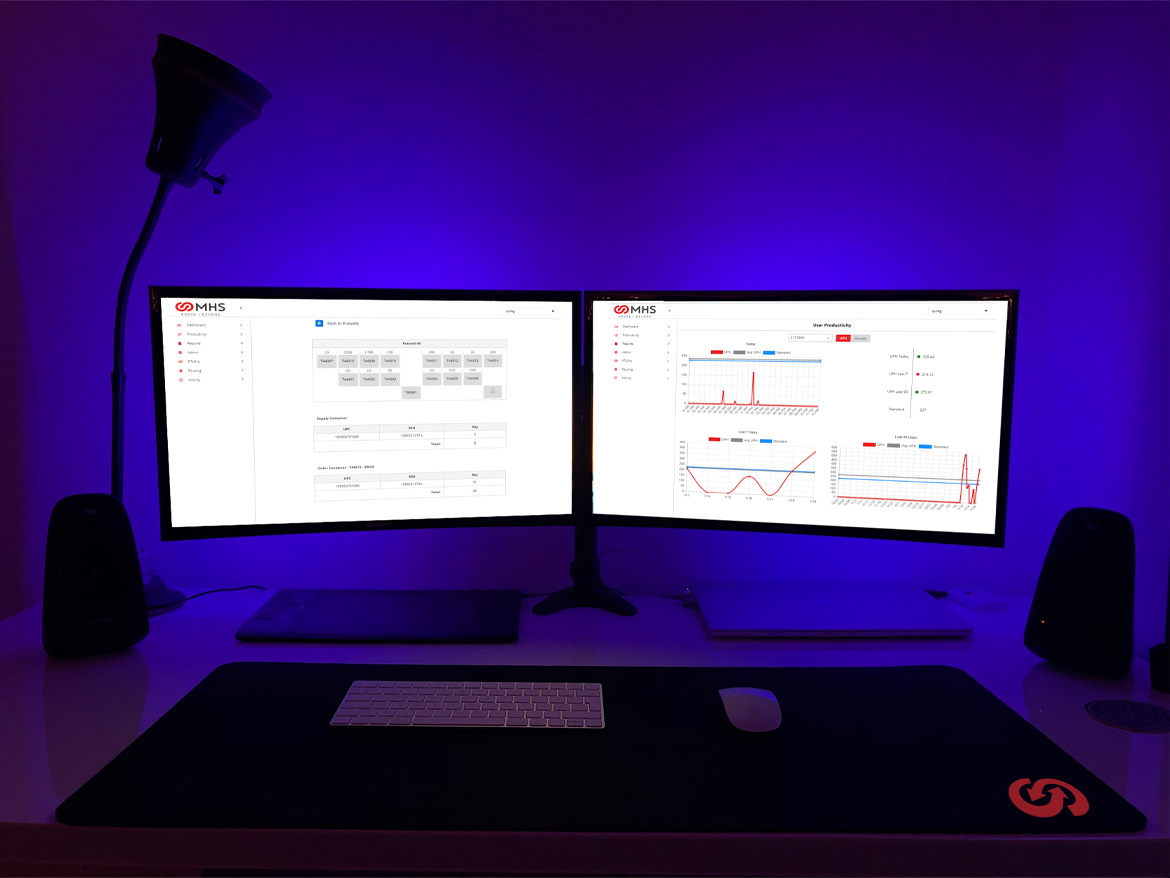
WES systems process client orders in an environment where the clients want smaller, faster and more frequent deliveries with the highest order accuracy
Image courtesy of MHS
Penned by Eagles’ singer-songwriters Don Henley, Glenn Frey and Randy Meisner, “Take it to the Limit” asks about the merits of spending time making money or spending love making time, while questioning if it “all fell to pieces tomorrow, would you still be mine?” The classic 1975 hit refrains to “put me on highway, and show me a sign,” and “take it to the limit one more time.” With burgeoning SKUs, more mixed pallets and packaging sizes, warehouses need to keep track of inventory and help warehouses “take it to the limit” to seamlessly accelerate fulfillment.
More than ever, warehouses must accomplish myriad tasks by utilizing warehouse management systems (WMS) in tandem with warehouse control systems (WCS), the software part of the equation, to sequence, manage and coordinate in real-time warehouse resources such as devices, material handling equipment and employees.
Today, WMS and WCS more commonly are compartmentalized under a different name: warehouse execution system (WES). The WES takes care that orders are moved in a continuous flow. When a situation changes in a single portion of the process, the system is expected to reprioritize work to accelerate fulfilment in today’s busy beverage warehouses or distribution centers.

Image courtesy of MHS
Although the business rules will differ between industries and customers, Francis Said, vice president of integration and engineering at DMW&H, Fairfield, N.J., likens wholesalers in the beverage industry to the retail industry.
“For example, when utilizing WMS and WCS systems, both still manage inventory, take orders from customers, cross reference the orders to the available inventory, generate work orders, and communicate to the WCS for real-time interface to the sub-systems,” he explains. “The sub-systems might look different since the product being handled is in fact different, but the same concept applies. The beverage industry does apply to different rules and regulations depending on each state, which dictates the logic to be implemented in the WMS/WCS.”
Experts note that WMS first emerged in the 1980s, when innovations like barcode scanning made real-time data collection much simpler and more affordable. Although beverage operations were largely manual 40 years ago, over time, WCS increasingly has taken greater control of the order fulfillment processes typically managed by WMS.
“This evolution stemmed from the reality that WCS was better positioned to make dynamic decisions requiring real-time status information from the equipment under its control,” explains Jennifer Tabbert, director of software sales for Atlanta-based Dematic Corp. “This shift eventually led to the emergence of a new term, WES (warehouse execution system) — a hybrid of WCS and WMS. WES empowers optimization of the overall material flow and order processing in concert, whether in one node or a series of nodes within a supply chain eco-system.
“Today’s WES systems are truly dynamic and real-time in nature, allowing for optimal flexibility in varying order profiles and volumes,” she continues. “This dynamism is especially true in complex integrated solutions, where WES manages all order fulfillment processes — from inbound to outbound. However, companies may still integrate WMS for inventory and order data, and then reprioritize and re-sequence operations to optimize the productivity of the system.”
She notes that some providers, like Dematic, have the capability to offer one holistic system to manage all processes — both within the warehouse and across the supply chain, offering a one-stop shop and maximum visibility.
Driving execution, ensuring order accuracy
In general, clients are using WMS and WCS systems to process client orders in an environment where the clients want smaller, faster and more frequent deliveries with a demand for the highest order accuracy. The systems also have evolved to include more advanced reporting and analytics than ever before, providing users the ability to see across their entire supply chain.
Given automation advances in warehouses, Bruce Bleikamp, director of product management for MHS, finds it hard to imagine a customer not having a WMS as a standalone product or one that is part of their enterprise resource planning (ERP) system.
“If you have automation equipment, you probably need a WCS/WES. The cost can be high, but the benefits are higher,” he says. “In automated systems, picking and order processing may be verified by scanners, scales and human operators every step of the way. Order accuracy will be very high and stock outages should be close to zero. Well-designed automated systems will, through the implementation of the WCS and the necessary equipment, deliver accuracy.”
The Mt. Washington, Ky.-based company offers the MHS Helix for WES operations. “The benefits of Helix include broad compatibility with a wide range of [application programming interfaces] APIs and data configurations, easy scalability and new workflows, secure browser-based access for visibility into inventory and orders, and a variety of communication and real-time reporting features,” Bleikamp says.
Specifically built from customer feedback in the beverage industry, DMW&H’s Shiraz Warehouse Control System covers all requirements needed including inventory management, wave creation, mix pallet creation, pick wave and picking, merge waves, ship waves, route assignments, order assignments, shipping door assignments and more. The system also prints labels, handles reporting along and provides exception handling.
“As the lines between tools blur, it is vital to understand which systems you should utilize and where to draw separations,” Dematic’s Tabbert says. “A specialized logistics and materials handling partner can help companies navigate this space.”
Before implementing a WMS/WCS system, Tabbert suggests companies consider the following factors:
- Volume — What volume is the company targeting, both now and in the next five to 10 years? How can warehouse software scale to those volumes? How does the software architecture support those volumes?
- Order profile — What are your order profiles like today? How will they change over the course of the next five years? How can warehouse software help to manage the varying demand and workflows associated with those different order profiles?
- Customer SLA — What promises are you planning to make to your customer(s)? How can warehouse software work to help you achieve those service level agreement (SLAs)?
- Level of automation — How much automation are you planning for? How can your warehouse software connect those islands of automation to help synchronize and balance the work based on the real time conditions of that hardware? How can software provide strong visibility into the health and status of the automation? How can software help with the support and maintenance of that equipment?
- Existing software ecosystem — What software exists in your network today that might impact this implementation? What upgrades/replacements do you have planned in the next five years? How can your warehouse software integrate into that existing network to reduce risk and customization? How can it help fill gaps created by your current software ecosystem?
- Network fulfillment strategies (dark store, BOPIS, urban fulfillment etc.) — What fulfillment channels do you operate in today? What new channels do you anticipate adding in the next five years? How can warehouse software help to streamline that process and reduce the number of touches and products in your ecosystem? How can the warehouse software provide visibility across your network?
In a web-enabled world that allows visibility from anywhere there’s Internet service, DMW&H’s Said advises that customers work with a qualified integrator from the design phase to achieve required results.
“DWM&H is the leading integrator for wine and spirits and has developed software and controls functionalities to meet these needs.” Said says. “From utilizing special components and logic, to performing and guaranteeing pick batches, sort batches, to managing bottle rooms and shipping doors. The WMS, WCS and controls systems are designed to work in harmony to deliver these results.”
Dematic’s Tabbert adds: “WCS/WES is the technology that allows the automation to ‘sing,’ per se. There will always be SKUs that can’t be handled by automation. This software, however, can make these manual tasks more efficient and balance work across both manual and automated processes to optimize performance and synchronization.”
With the industrial internet of things (IIoT) and automation pacing today’s beverage warehouse operations, tightly integrated WMS and WCS systems will continue to evolve, particularly as the market is ripe for innovation.
According to Research and Markets, the global warehouse execution system market is expected to reach $2.5 billion by 2027, rising at a compound annual growth rate (CAGR) of 12.3% from 2021-2027
“Automation is a key factor to meeting some of these demands, starting with conveyors, to sorters, to shuttle systems and followed by robotics and AMRs,” DWM&H’s Said says. “As the automation evolves to meet the industry demands, so does the WMS/WCS systems, which will need to keep up with the beverage industry and the automation [that] enables a beverage plant’s success.”
Looking for a reprint of this article?
From high-res PDFs to custom plaques, order your copy today!