Beverage storage systems continue to be driven by automation
AS/RS operations accommodate increased SKUs
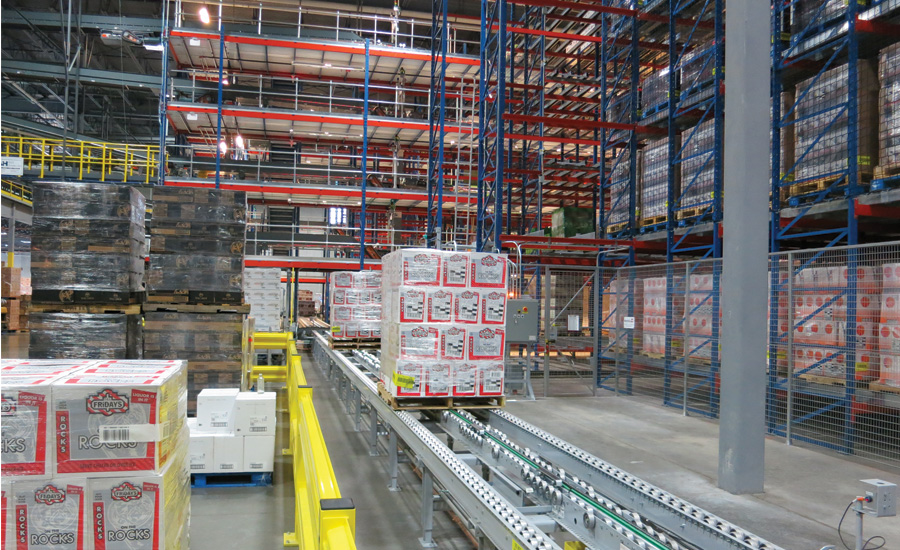
Chicago-based Mintel’s Global New Products Database shows that between January 2015 and January 2016, 5,226 new beverages were launched in North America. In fact, similar numbers of launches were recorded over the past five years. As beverage manufacturers continue to pump out these products, distributors have had to find ways to accommodate the growing number of SKUs. For many warehouses, automation is the cornerstone of their operations as they keep pace with their growing inventories.
Aaron Corcoran, account executive at Westfalia Technologies Inc., York, Pa., notes that SKU proliferation has been impacting warehouse storage systems for the past decade. “As SKU growth continues, it brings a change with it that affects the warehouse in other ways, more complex customer orders,” he says. “While in the past, most customer orders were made up of full pallets of one SKU, or pallets with multiple layers that each contained one SKU, now orders are going down to the case level. This creates a larger and more complex area needed for creating these orders. More SKUs, either in pallet form or in case-flow racking, need to be presented to picking operators to fulfill the customer orders. As this complexity grows, companies are looking to automation in different ways to maximize their impact.”
Automation consideration
Although warehouse automation is not a new concept, industry growth has made it a higher priority for some growing distributors. “[E]ach facility, depending on size, should look to automate to some degree,” says Tom Steininger, market development director of food and beverage at Dematic Corp., Grand Rapids, Mich. “The automation should be scalable and grow with the business. …Each facility is unique, [and] the data needs to drive the solution and determine the [return-on-investment] (ROI).”
He notes that automated storage solutions can assist with more than just space-saving. He highlights customer-specific order lines, labor reduction, inventory control and visibility, order accuracy, and picking efficiency as factors with which automated storage solutions can assist.
Arden, N.C.-based ITW Warehouse Automation’s (ITWWA) Vice President of Sales and Marketing John Barry echoes similar sentiments. “It’s all about driving out costs,” he says. “[The] keys are labor, costs and availability, storage costs [and] delivery costs.”
According to Barry, key trends dominating beverage storage systems are deep-lane storage; automated replenishment for picking; and case-buffering for palletizing, slow-movers and top-off, which offer increased benefits to automated warehouses. He adds that layer handling has been a focus as well as case handling, each picking and goods-to-person for each/bottle picking.
Chris Lingamfelter, vice president of integrated systems sales and strategy for Mason, Ohio-based Intelligrated, notes similar benefits. “Automation has provided the beverage industry with a method to handle a wide variety of packaging and new SKUs,” he says.
“Lower labor costs, utilization of the entire storage cube of the building and high throughput to fill orders in a shorter period of time [all are benefits],” he adds.
However, automation might not be the answer for every warehouse. A warehouse should consider several factors when determining whether to automate or maintain a non-automated storage system. “This is the most critical question to answer when looking into automation and the unanimous answer is, chose an automation partner that takes the time to understand your business and develop the right level of automation for your specific needs,” Westfalia’s Corcoran says. “Too many times automation suppliers focus on fitting their systems into a customer’s needs and the end result is a system [that] the customer is not satisfied with. …We ensure we understand the customer’s business and needs before we begin to discuss automation opportunities.
“…Automation and [automated storage and retrieval systems] (AS/RS) do bring change to any business they are brought into,” he continues. “The open and honest partnership of discussing current business practices and how those will blend with applying automation to your business is the key to success. The day an AS/RS system is put into working production for a customer is only made successful by ensuring the early stages of the idea of automation is embraced by the culture of the end-user. Automation can accomplish many tasks, but will only be successful by the collaboration of its creators.”
Intelligrated’s Lingamfelter notes that the decision also should be based on storage space and throughput. “If a building is landlocked and there is no room to add more space, you must utilize the space available,” he says. “Likewise, if you need a high throughput system with rates that exceed human capacity, then you need to automate.”
Making accommodations
AS/RS solutions are touted by experts to help accommodate the dominating trend of increased SKUs. “An AS/RS can provide vertical storage, enabling operations to use the entire cube of the building. Thus, increasing the capacity of the building,” Lingamfelter explains.
Westfalia’s Corcoran adds that companies are building upon their AS/RS operations. “As AS/RS becomes more widespread in the beverage industry, it brings along with it the natural progression of applying a warehouse execution system (WES) to many companies. These systems provide another level of automated data visibility to many warehouses that they did not have before,” he says. “When combined, the AS/RS and WES partnership brings with them a business process maturity that many beverage companies are looking for.”
He highlights Westfalia’s Savanna.NET WES, an integrated warehouse management system (WMS) and warehouse control system (WCS). “WES has changed the way many companies view their businesses and manage their daily warehouse activities,” he says. “Savanna.NET’s ability to interface with [the] current customer system and ability to integrate customer business rules has made the switch to AS/RS far easier than one would expect.”
He also notes that the company’s AS/RS and case packing and handling equipment support the needs of today’s beverage warehouse. “Our Satellite technology allows multiple pallets, up to 18 deep, to be stored in one lane [and] aligns well with the typical storage requirements of the beverage industry,” he says. “This feature, along with our tandem Satellite retrieval system, provides our customers with the ability to traverse multiple levels of a storage system with one piece of equipment in comparison to other technologies.”
Storing tomorrow
As consumers continue to demand new, innovative beverage products, warehouses will need to continue to innovate in order to support more and more SKUs. ITWWA’s Barry notes that flexibility for handling all types of units, including pallets, layers, cases and eaches, to support changing business demands will develop in the future. “[The changing demands are] created by omni-channel distribution driven by more demanding customers and suppliers,” he says.
However, he also notes that automation innovation for storage will require further change. “Our customer’s skill level to support their new automation systems is going to have to get better,” he says. “They are going to have to hire a new breed of employee — more technically skilled.”
Yet, the future remains bright for automation and specifically AS/RS within beverage warehouses, according to Wesfalia’s Corcoran. “We have seen, over the last several years, the industry is becoming more aware of the abilities and advantages of AS/RS systems,” he says. “Based on this, the future is bright for a great partnership between AS/RS systems and the beverage industry.”
Looking for a reprint of this article?
From high-res PDFs to custom plaques, order your copy today!