Refrigeration options for beverage fleets expand
End-load trailers and body contribute to expansion
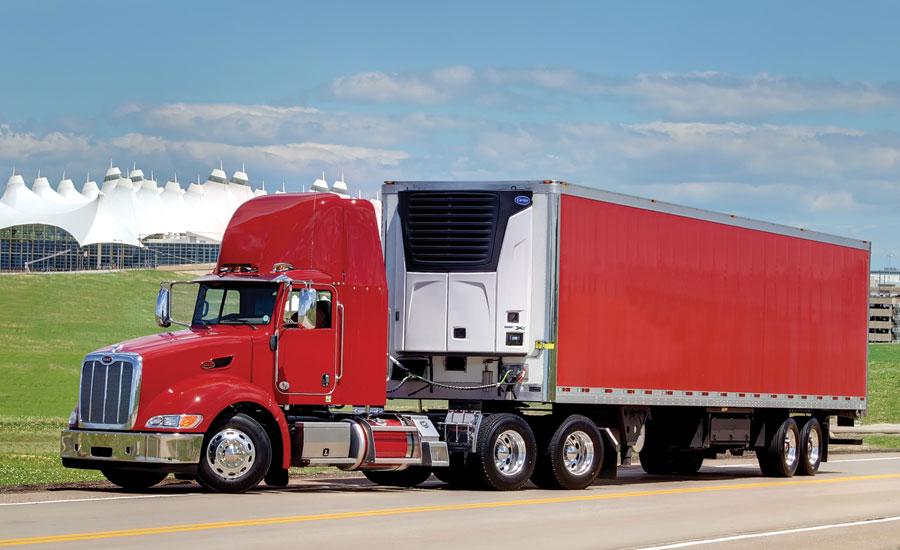
Back when side-load equipment ruled the beverage industry, refrigeration generally was an afterthought, with just a few refrigerated trucks dedicated to delivering dairy products and limited varieties of draft beer. But as product mixes have expanded, a paradigm shift is taking place in the equipment world.
Side-load equipment always has been tough to configure for refrigerated cargo, even with a mix of roll-up doors and swing doors on a “hybrid” trailer. But as SKU proliferation has led to preselling and palletizing of orders, the result has been a major shift to end-load bodies and trailers that open up a wide range of off-the-shelf refrigeration solutions for beverage delivery.
A wide selection of standard refrigeration equipment is another factor driving the shift toward end-load bodies and trailers.
Traditionally, transport refrigeration was a “yes” or “no” proposition. If the commodities being hauled included dairy, juice or draft beer, refrigeration was specified, but many other products typically have been moved without refrigeration. As such, most fleets either were entirely refrigerated, non-refrigerated or operating with just a few refrigerated units.
Blurring lines
Taking into account distributor consolidation, SKU proliferation and distributors expanding their product portfolios, the need for transport refrigeration is becoming less clearly defined.
Similarly, on the equipment side, the line between unrefrigerated equipment and refrigerated equipment is becoming equally unclear.
When starting with an uninsulated body or trailer, the first step to maintaining cargo temperature is upgrading to insulated equipment. In moderate climates, insulated equipment can move pre-chilled cargo across short distances with little temperature change.
At the opposite end, purpose-built refrigerated bodies and trailers are available with multiple insulation options to meet interior and exterior temperature demands.
Unlike truck bodies, which either can use cold-plate or mechanical refrigeration, trailers primarily use mechanical refrigeration. This mainly is because of the volume of space being refrigerated, and the need for self-contained operating units.
Entry-level trailer refrigeration units have long used a small-diesel engine to mechanically drive a refrigeration compressor and small alternator. Given an ample supply of fuel, this type of unit can keep a trailer and its cargo cold for extended periods of time, but this capability comes with many downsides.
Mechanically driven compressors are much more prone to leaks than sealed compressors, and the exhaust and noise emissions from the diesel engine can be objectionable when the trailer is parked in public locations for extended periods.
Hybrid power adds benefits
Making a break between the engine and compressor, newer trailer refrigeration units use a larger alternator directly coupled to the engine, which electrically runs the entire refrigeration system.
Not only does this enable the use of a low-maintenance, sealed compressor, but it also simplifies running the refrigeration unit on shore power when docked or parked for extended periods, cutting exhaust and noise emissions, saving fuel, and reducing engine wear.
A comparatively recent solution for distributors serving large events, or seasonal peaks in the retail segment, are trailer refrigeration units that run on shore power alone. The Vector 8100 from Carrier Transicold shares most of the technology of its diesel-electric hybrid-equipped Vector siblings, but omits the diesel engine used to power the refrigeration system en route, which saves both cost and weight.
A distributor can pre-position bulk product using a trailer equipped with an electric-only unit like the Vector 8100 to serve as cold-storage at the venue location, running cleanly and quietly on shore power.
However, no matter how it’s powered, another major consideration when choosing a refrigeration unit is the number of temperatures it will need to maintain. Dairy distributors might already be familiar with “multi-temp” refrigeration, used to carry frozen, refrigerated and dry products all in one load.
By using a trailer equipped with fixed or movable bulkheads and a multi-temperature-capable refrigeration unit, a distributor entering a chilled segment easily can deliver products with one body/trailer.
However, keeping products cool or cold isn’t always the only goal. In many northern states, hauling some types of beverages during the winter might entail preventing cargo from freezing. Sometimes freeze prevention can be accomplished with insulation alone, but in colder climates, adding heat might be necessary.
As product mixes and beverage delivery options continue to evolve, there’s an increasingly wide range of new refrigeration options available for end-load bodies and trailers. The flexibility offered by these options can bring added versatility to your fleet.
Looking for a reprint of this article?
From high-res PDFs to custom plaques, order your copy today!