Filling equipment focuses on total cost of ownership
Flexibility, sustainability features help support beverage-makers' bottom lines
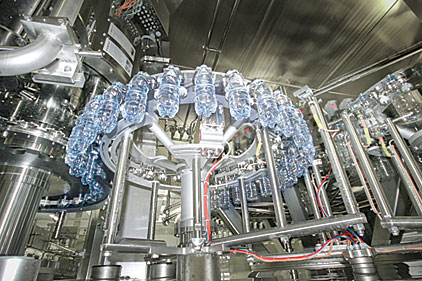
In boxing, a TKO indicates a technical knockout that officially ends the fight. For beverage manufacturers competing “in the ring,” it’s the TCO that drives much of the battle in regard to filling equipment. Achieving the best total cost of ownership (TCO) might help a beverage-maker “win” financially, but many other factors come into play that challenge operators to meet changing demands in the beverage market — both financially and operationally.
![]()
|
Better TCOs and quicker returns on investments (ROIs) are among the most common customer requests, says Barry Fenske, product manager for filling technology at Krones Inc., Franklin, Wis. However, these requests are joined by demand for flexibility, faster changeovers, down-weighting bottles and caps, and better efficiencies, he notes.
Flexible strategies
“Whether it’s beer, water, juice, [carbonated soft drinks] (CSDs), hot-fill, cold-fill, carbonated, non-carbonated, their own label, or co-packed, customers want more flexibility,” Fenske says.
In fact, multiple filling machine manufacturers have identified flexibility as a key trend within the beverage industry.
“Flexibility is a key aspect as the market is more and more demanding,” says Federico Zannier, filling lines global sales manager for SIPA SpA, Vittorio Veneto, Italy. “It’s now time to rethink the manufacturing platform [and switch] from a ‘rigid’ to a ‘flexible’ system. Production lines should be able to deliver the real mix needed by consumers.”
This demand for flexibility applies to packaging formats, beverage types and changeovers, he notes. To meet this need, SIPA developed its Flextronic range of modular volumetric fillers, which allow bottlers to fill multiple products on the same line, Zannier says. Flextronic C, for instance, can handle carbonated, still and hot-fill beverages with or without pulp as well as a variety of containers with different neck sizes, he notes.
The same flexibility applies to can-filling machines, notes Ed Ruble, engineering manager for Adcor Packaging Group LLC, Baltimore.
“The introduction of multiple can sizes and products has made a significant impact on can filler users’ requirements,” he says. “They need the flexibility to run [cans with various] lids, diameters and heights.”
Therefore, Adcor has adapted its can fillers accordingly by adding improved elevating systems to accommodate can heights and developing quick-change handling parts to help facilitate faster and more efficient changeovers from can to can, he says.
From mechanical to electronic
Shifting filler control systems from mechanical to electronic also enables flexibility and hastens changeovers, suppliers note. For instance, integrating electronic level and pressure control and temperature systems within beverage process systems and line controls improves and automates the running of both hot- and cold-fill products on the same equipment, Ruble says.
Filamatic, a Baltimore-based division of National Instrument, incorporates servo controls and sensors in its filling machines in a variety of areas, which allow its customers to change recipes quickly, says Aaron Saxton, director of sales and marketing for the company.
“Our machine design allows for a range of bottle sizes that typically allows customers to not require a significant number of tooling changes,” he says. “When a tooling change is required, we emphasize toolless changeover wherever possible.”
Similarly, Krones revamped its fillers’ drive trains and replaced the gears with servo motors, Fenske notes.
KHS USA Inc., Waukesha, Wis., has eliminated numerous mechanical devices within its current filling equipment technology and instead primarily operates electro-pneumatically, says Bob Pease, director of the company’s wet-end product group.
“Therefore, machine functions are executed by simple pneumatics, as controlled by [the] machine’s filling computer,” he explains. “There is no guesswork or interaction by [the] operator; the computer programs may be preset for various packages or products; and the changeover is therefore automatic, precise and instantaneous.”
For SIPA, incorporating electronic management into the entire filling process enabled it to yield a global reduction in power consumption, it says. Consumption of carbon dioxide when filling carbonated drinks and product loss from the snift circuit also are reduced, it adds.
“We perceive a trend where fillers should not only be fast and precise, but the focus is more and more on economic aspects, meaning low energy and carbon dioxide consumption, quick changeovers (and therefore less downtime for changeovers) and, in general, the best TCO,” SIPA’s Zannier says.
Additionally, many filling machines now fill bottles or cans volumetrically, KHS’ Pease notes. “The benefits, in addition to better yields, are elimination of changeover-intensive hardware, such as vent tubes, [which were] previously required for fill-to-a-level processing,” he says. “This reduces both changeover and sanitation time.”
Elihu Rivera, sales engineer at Universal Packaging, affirms this trend, noting that volumetric fillers are becoming more prevalent in the industry. As a result, the Orange City, Fla.-based company has been working on a new volumetric filling valve for bottle-filling machines, he says.
Changing pace
Quickening the speed of changeovers also has become increasingly important as changeovers become more frequent because of beverage SKU proliferation, KHS’ Pease notes.
As a result, Filamatic introduced fast changeover piston pumps within the past year, Saxton notes.
Universal Packaging also has improved its filling valves over the years to accommodate this trend. “Whether it’s a filling valve that requires a [clean-in-place] system, quick-change vent tubes for faster changeovers, or designing a filling valve that fills products with pulp, we try to fulfill the needs of our customers within the ever-changing industry,” Rivera says.
Maintaining good hygiene
In addition to customer demands for flexibility, sustainability and faster changeovers, filling equipment must be hygienic, suppliers note. Many times, this means upgrading or incorporating designs that make use of stainless steel, Adcor’s Ruble says.
For instance, SIPA’s Flextronic range was created with valves made of stainless steel. The valves were designed so that they could be separated and cleaned without having to disassemble the entire valve, Zannier notes. The range also was designed with a clear separation between the pneumatic components and the parts in contact with the product in order to avoid contamination, he says.
Late last year, Norcross, Ga.-based Sidel added a hot filler to its Sidel Matrix range that boasts contactless filling valves. As a result, the product never comes into contact with the ambient air, and the bottle never comes into contact with the filling valve, the company notes. Therefore, the risk of cross-contamination is reduced.
Krones’ Fenske also notes that the company designs its entire product path to ensure that proper cleaning can take place in order to protect whatever the operator is going to fill. It also can incorporate foaming systems that clean the exterior of the machine, he adds.
Additionally, sloped machine surfaces can prevent standing liquids, KHS’ Pease notes. Minimizing external machine elements also can eliminate clutter and reduce sanitation targets. Internally, product contact channels that are designed to allow high flow rates and no product-trapping surfaces can facilitate rapid and thorough sanitation, he adds.
As the beverage industry changes and evolves, efficiency also becomes increasingly important, Universal Packaging’s Rivera notes. As a provider of high-speed replacement aftermarket filling valves, Universal receives many inquiries regarding increasing filling speeds, he adds.
“As new shapes, sizes and lighter bottles become more prevalent, higher demands require us to design ways to fill bottles more efficiently,” he says.
In the future, Rivera expects to see better and faster volumetric filling machines as well as fully automated bottling lines that are regulated and maintained by a control center.
Looking for a reprint of this article?
From high-res PDFs to custom plaques, order your copy today!