Promoting safe driving
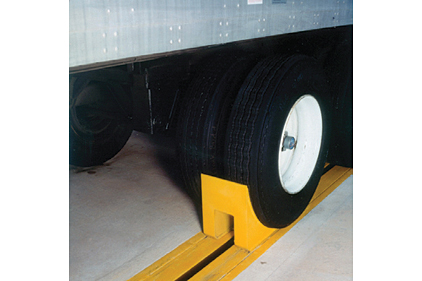
A primary duty in most management positions is controlling costs. For a beverage fleet manager, this can be a tough task. It’s definitely possible to incrementally control costs by getting the most longevity out of trucks and tires as well as getting the most distance out of a gallon of fuel. But most areas of potential cost control in a beverage fleet amount to a game of inches, not yards. Ultimately, moving a given weight and volume over a fixed distance doesn’t afford many opportunities to make a wholesale reduction in costs.
![]() |
In-ground wheel restraints, such as the Universal Truck-Chock System from Serco, provide continuous restraining force to the chocked wheel, reducing the accident frequency associated with landing gear collapse, vehicle creep or vehicle walk. |
One area where fleet costs can and should be significantly reduced, if not eliminated, is vehicular accidents. At first glance, reducing the cost and frequency of accidents might seem to strictly be a matter of driver training and incentives, but in reality, there are many ways a manager can reduce or eliminate the potential for accidents before a driver ever gets behind the wheel.
There’s often a repeated admonition in the automotive safety world that says most accidents happen within 25 miles of home. For many distribution fleets, that distance can be considerably shorter. Many accidents happen before the truck ever leaves the dock, due to insufficient dock safety equipment and practices.
Numerous factors can cause a truck or trailer to move away from the dock as forklifts and pallet jacks travel in and out. Anything from simple inertia when a forklift comes to a stop to vertical forces acting on the truck/trailer suspension can cause progressive movement away from the dock. This can result in a serious injury accident if a forklift or pallet jack falls off the dock.
Parking brakes generally are not sufficient to prevent movement of the trailer while loading, nor are portable wheel chocks completely fail-safe. Fortunately, there are a few ways to secure the truck/trailer from moving during loading.
One of the most common systems involves a dock-mounted hook that engages the truck/trailer ICC (ride-under) bar to prevent movement away from the dock. However, these hook systems might not be compatible with many types of lift gates. The alternative is to use a permanently mounted wheel restraint system. Although these systems look similar to a wheel chock, they are built into the loading ramp area, staying level with the pavement until the operator sets the restraint electrically, raising it out of the ground and moving it against the truck/trailer tires.
Just as proper dock safety can prevent an accident before the truck ever leaves the yard, many spec’ing choices are available that, if made before the truck ever hits the road, can help prevent accidents. Fleets operating in crowded urban areas should consider the maneuverability and visibility offered by a truck to be just as important as horsepower and capacity.
Many distributors are shifting away from straight-trucks on their larger routes in favor of tractor-trailer combinations, which can dramatically improve maneuverability compared with a straight-truck of similar capacity. This added maneuverability greatly reduces the potential for low-speed collisions in loading and parking areas.
Now that domestic truck manufacturers are displaying a newly restored interest in cabover style trucks, leading fleet operators are beginning to adopt this nimble configuration on some lower-volume routes. In addition to providing the ultimate in maneuverability with shorter wheelbases, the cabover configuration eliminates the large “nose” found on conventional-cab trucks, providing far better visibility when operating in tight quarters and all but eliminating forward blind-spots. The added visibility can significantly reduce the potential for low-speed accidents.
Another increasingly popular shift in truck configurations is to choose end-load bodies and trailers instead of the traditional side-loaders used in the beverage industry. By eliminating the need for drivers to be on the street-side of a truck to pick an order, the possibility of accidents where the driver is struck by traffic can be reduced.
For trucks used on longer routes where operating at freeway speed is a regular occurrence, many of the truck original equipment manufacturers (OEMs) offer electronic stability/roll-stability systems that automatically engage the vehicle’s anti-lock braking system to correct for loss of directional control and to avoid potential rollover scenarios. The stability control systems still deliver benefits even during lower speed operation where traction is limited due to ice or other poor surface conditions.
Most top fleet managers in the beverage business have a system of one kind or another for training drivers to minimize preventable accidents. Each company’s operating environment is unique, and thus each training system is likely to be unique as well but should feature a number of proven core elements common to any driver safety training system.
One of the most time-proven driver safety training programs is the Smith System. Originally developed in 1952 as the “Smith System of No Accident Driving,” it is based on five key elements: aim high in your steering; get the big picture; keep your eyes moving; make sure they see you; and leave yourself an out. Today, the Smith System Driver Improvement Institute offers numerous resources to support driver safety training programs. BI
Looking for a reprint of this article?
From high-res PDFs to custom plaques, order your copy today!