Making inventory tracking more ‘pallet-able’
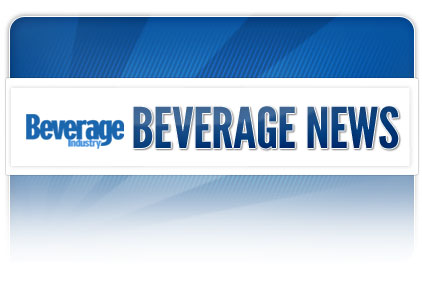
As New Belgium Brewing Co., Fort Collins, Colo., celebrated its 20th anniversary in 2011, the craft brewery had grown from brewing 60 cases a week at the home of co-founders Jeff Lebesch and Kim Jordan in 1991, to selling more than 700,000 barrels of beer a year. When the co-founders created what Jordan calls their “magical experiment,” they compiled a list of the company’s core values and beliefs that would be used to guide them on their journey, including “Continuous, innovative quality and efficiency improvements.”
In 2000, after a number of years of contemplation, New Belgium’s principals made the pivotal decision to capitalize on the increasing popularity of their beers and initiate a continuous growth strategy for the company and its brands. This full-speed-ahead approach created the need for more efficient and reliable inventory tracking in its production, bottling, warehousing and shipping operations.
To aid them in maximizing this critical business decision, New Belgium turned to Markem-Imaje, Kennesaw, Ga., a manufacturer and distributor of industrial coding and marking equipment. One of the first pieces of equipment that Markem-Imaje provided New Belgium was a CimPak Pallet Labeler that was used to place pre-printed license plate inventory labels (LPNs) on stretch-wrapped pallets of beer as they were coming off the bottling lines.
As New Belgium’s operation grows, so do the challenges in inventory tracking. Until recently, the company’s pallet labels included multiple bar codes that needed to be scanned in the proper sequence so that the correct information could be transferred to its Microsoft Great Plains Enterprise Resource Planning (ERP) and Warehouse Management System (WMS) programs, which were responsible for recording and tracking the inventory for each of the beer brands.
However, inefficiencies often would arise during peak production times when the bar codes were not scanned in the proper sequence required by the Great Plains ERP and WMS programs. Also, if the information on a label was incorrect, the operator would need to initiate a separate Great Plains process that would correct the inventory levels and print a new LPN that would then need to replace the incorrect one.
The solution
Working again with Markem-Imaje, New Belgium created a two-phase blueprint for upgrading the inventory management system that would focus first on the existing bottling line and then on a new keg-filling line. The success of the project revolved around the implementation of a new single-label LPN template for both the bottling and keg lines. At the heart of the new inventory-tracking system is Markem-Imaje’s CoLOS software package that creates basic date and lot code images that are compatible with all Markem-Imaje printers, as well as Datamax-O’Neill printers, according to the company.
The CoLOS product line is composed of two core types of coding software: one dedicated to message design and printer network control, and another focused on traceability, which provides additional plug-in functionalities such as coding integrity, pallet tracking and line traceability solutions.
The CoLOS system that Markem-Imaje developed for New Belgium revolves around the Pallet Track software that features a single scannable field on the LPN that is placed on the pallet label. All other product identification information is passed from CoLOS to the Great Plains ERP system electronically via a bi-directional open database connectivity (ODBC) link.
After the LPN has been applied to the pallet, a laser scanner verifies that it has been applied correctly and the CoLOS Pallet Track software transmits the LPN number via the ODBC to the Great Plains ERP SQL database where the actual inventory is created and the storage or shipping information is uploaded. The integration with the Great Plains ERP system informs CoLOS Pallet Track which batch is being packaged on each line while simultaneously allowing CoLOS to communicate the inventory creation as soon as the LPN is applied to the pallet.
The use of the Markem-Imaje CoLOS Pallet Track solution also provides New Belgium with the ability to tie a specific serial number directly to its quality-assurance grading data. This information is automatically printed on the LPN, which is then applied to one side of all stretch-wrapped pallets. New Belgium also is able to access the CoLOS database via the ODBC report writer, giving operators the ability to create and print specific inventory reports as needed.
CoLOS helped New Belgium improve its inventory accuracy and overall productivity by ensuring that the correct production information is communicated in real-time to its Great Plains ERP system on a pallet-by-pallet basis and by printing LPNs “just in time” and with the correct information through a unique labeling process that eliminates the need to manually apply them or adjust inventory levels within the Great Plains ERP program as a result of incorrect scanning sequences, according to Markem-Imaje. BI
Markem-Imaje is a world manufacturer of product identification and traceability solutions, offering a full line of reliable and innovative inkjet, thermal transfer, laser, print and apply label systems and RFID-based systems. Markem-Imaje delivers fully integrated solutions that enable product quality and safety, regulatory and retailer compliance, better product recalls and improved manufacturing processes. Additionally, Markem-Imaje customers are supported by six research and development centers, and several equipment repair centers and manufacturing plants strategically located around the globe. For more information on Markem-Imaje, visit
Looking for a reprint of this article?
From high-res PDFs to custom plaques, order your copy today!